Kuidas parandada sferoidiseerumiskiiruse valamisprotsessi mõõtmeid
Kodumaiste tavaliste sferoidgraafiidist malmist valandite sferoidiseerumistase on vajalik 4. või kõrgema taseme saavutamiseks (see tähendab, et sferoidiseerimise määr on 70%), üldise valukojaga saavutatud sferoidiseerimise määr on umbes 85%. Viimastel aastatel on nodulaarse malmist tootmise arenguga, eriti tööstustes, kus tuuleelektrijaama valamise tootmine ja valamise kvaliteet on kõrgete nõudmistega, sferoidiseerumise tase on vajalik 2. taseme saavutamiseks, see tähendab, et sferoidiseerumise määr ulatub üle 90%. Autori ettevõte analüüsis ja täiustas QT400-15-s kasutatud sferoidiseerimis- ja inokuleerimisprotsessi, samuti sferoidiseerivat ainet ja inokulanti, nii et nodulaarse malmi sferoidiseerimise määr ulatus üle 90%.
1. Algne tootmisprotsess
Algne tootmisprotsess:
- Sulatusseadmetes võetakse kasutusele 2.0T vahesagedusahi ja 1.5T tööstussagedusahi;
- QT400-15 toore rauavedeliku koostis on ω (C) = 3.75% ~ 3.95%, ω (Si) = 1.4% ~ 1.7%, ω (Mn) ≤0.40%, ω (P) ≤0.07%, ω (C S)) ≤0.035%;
- Sferoidiseerivas töötluses kasutatav sferoidiseeriv aine on 1.3% kuni 1.5% RE3Mg8SiFe sulamit;
- Inokuleerimisel kasutatav inokulant on 0.7% ~ 0.9% 75SiFe-C sulamit. Sferoidiseerivas ravis kasutatakse kahte koputus- ja loputusmeetodit:
Esiteks toodetakse rauast 55–60%, seejärel sferoidiseeritakse, seejärel lisatakse inokulant ja seejärel ülejäänud rauavedelik.
Traditsioonilise sferoidiseerimise ja inokuleerimise meetodi tõttu on 25 mm paksuse ühe valatud kiilkatse abil tuvastatud sferoidiseerimise määr tavaliselt umbes 80%, see tähendab, et sferoidiseerituse tase on 3..
2. Testimiskava sferoidiseerumise määra parandamiseks
Sferoidiseerumise määra suurendamiseks on parandatud algset sferoidiseerimis- ja inokuleerimisprotsessi. Peamised meetmed on: sferoidiseeriva aine ja inokulandi koguse suurendamine, sulanud raua puhastamine ja desulfureeriv töötlemine. Sferoidiseerumise määra testitakse endiselt ühe valatud kiilukatsega 25 mm. Konkreetne plaan on järgmine:
- (1) Analüüsige algse protsessi madala sferoidiseerumise määra põhjust. Arvati, et sferoidiseeriva aine kogus oli väike, seetõttu lisati sferoidiseeriva aine kogust 1.3% -lt 1.4% -le 1.7% -le, kuid sferoidiseerimisaste ei vastanud nõuetele. . (2) Teine oletus on see, et madala sferoidiseerumise määra võib põhjustada kehv rasedus või viljakuse langus. Seetõttu suurendas katse inokuleerimise annust 0.7% -lt 0.9% -le 1.1% -ni ja sferoidiseerumise määr ei vastanud nõuetele.
- (3) Jätkake analüüsi ja uskuge, et sulatatud rauas on rohkem lisandeid ja madala sferoidiseerumise määra põhjuseks võivad olla suured sferoidiseerumise interferentselemendid. Seetõttu viiakse sulatatud raua puhastamine kõrgel temperatuuril. Kõrge temperatuuriga puhastustemperatuuri reguleeritakse tavaliselt temperatuuril 1500 ± 10 ° C, kuid selle sferoidiseerumiskiirus ei ole ületanud 90%.
- (4) Suur ω (S) kogus kulutab sferoidiseerivat doosi tõsiselt ja kiirendab sferoidiseerimise langust. Seetõttu suurendatakse väävlitustamist, et vähendada algse rauavedeliku ω (S) kogust 0.035% -lt vähem kui 0.020% -le, kuid sferoidiseerumise määr on samuti ainult 86%. Ülaltoodud nelja skeemi katsetulemused on toodud tabelis 1. Kiilukujulise katseploki struktuur ja mehaanilised omadused ei vastanud nõuetele.
3. Viimane vastuvõetud parendusplaan
3.1 Spetsiifilised parandusmeetmed
- Tooraineks on malm, roostevaba või vähem roostes vanaraua ja uuesti kuumutamise materjalid;
- Toore sulanud raua desulfureerimine, lisades ahju sooda (Na2CO3);
- Kotis eeloksüdeerumiseks kasutage Foseco 390 eeltöötlusainet;
- Sferoidiseeriv ravi Fozco Nodulizeriga;
- Ränikarbiidi ja ferrosilika kombineeritud inokuleerimise kasutamine.
Uue protsessi algse sulanud raua koostise kontroll: ω (C) = (3.70% ~ 3.90%, ω (Si) = 0.80% ~ 1.20% [valamine ω (Si lõplik) = 2.60% ~ 3.00%], ω ( Mn) ≤ 0.30%, ω (P) ≤0.05%, ω (S) ≤0.02%. Kui algne sulanud raud ω (S) ületab 0.02%, kasutatakse ahju ees väävlitustamiseks tööstuslikku sooda, kuna desulfureerimisreaktsioon on endotermiline reaktsioon. Vääveldustemperatuuri tuleb reguleerida umbes 1500 ° C juures ja lisatud sooda kogust reguleeritakse ahjus sulatamise ajal 1.5% ~ 2.5% vastavalt ω (S) kogusele. .
Samal ajal võtab sferoidiseeriv ravipakett tavalise tammi tüüpi ravipaketi. Esmalt lisage pakendi põhjas oleva tammi küljele 1.7% Foseco NODALLOY7RE kaubamärgi sferoidiseerivat ainet, lamendage ja tihendage ning kasutage 0.2% pulbrilist ränikarbiidi ja 0.3% väikest. 75SiFe mass on kaetud ühe kihiga üksteise järel ja pärast tampimist kaetakse see survrauduga ning sulatatud rauakulbi teisele küljele lisatakse 0.3% inokulant Foseke 390. Raua koputamisel loputatakse kõigepealt 55% ~ 60% kogu sulanud raua mahust. Pärast sferoidiseerimisreaktsiooni lõppu lisatakse 1.2% 75SiFe-C inokulanti, ülejäänud sula raud pestakse ja räbu valatakse.
3.2 Katse tulemused
Algse sulanud raua koostis enne ja pärast väävlitustamist, 25 mm ühe kiilukujulise katseploki mehaanilised omadused ja metallograafiline struktuur ning metallograafilise struktuuri sferoidiseerumiskiiruse hindamismeetod tuvastatakse metallograafilise pildi analüüsisüsteemi abil automaatselt .
4. Tulemuste analüüs
4.1 Põhielementide mõju sferoidiseerimise määrale
- C, Si: C võib soodustada grafitiseerimist ja vähendada suu valgekalduvust, kuid suur hulk ω (C) muudab CE liiga kõrgeks ja põhjustab hõlpsasti grafiidi hõljumist, kontrollides seda tavaliselt 3.7–3.9%. Si võib tugevdada grafitiseerimisvõimet ja kõrvaldada tsementiiti. Kui inokulandina lisatakse Si, võib see oluliselt vähendada sula raua ülekuumenemise võimet. Inokuleerimisefekti parandamiseks vähendati ω (Si) hulka algses sulatatud rauas 1.3% -lt 1.5% -lt 0.8% -le kuni 1.2% ja ω (lõpliku Si) kogust kontrolliti 2.60% kuni 3.00%.
- Mn: kristallimisprotsessi ajal suurendab Mn malmi kalduvust ülejahtuda ja soodustab karbiidide (FeMn) 3C moodustumist. Eutektoidse transformatsiooni protsessis vähendab Mn eutektoidse transformatsiooni temperatuuri, stabiliseerib ja rafineerib pärliiti. Mn ei mõjuta sferoidiseerumise määra eriti. Tooraine mõju tõttu on kontroll ω (Mn) üldiselt <0.30%.
- P: kui ω (P) <0.05%, lahustub see tahkesti Fe-s ja fosfori eutektikat on raske moodustada, millel on vähe mõju kõrgtugeva raua sferoidiseerumiskiirusele.
- S: S on desferoidiseeriv element. S kulutab sferoidiseerimisreaktsioonis sferoidiseerivas aines Mg ja RE, takistades grafitiseerimist ja vähendades sferoidiseerumise kiirust. Enne sulanud raua tahkumist naaseb sulfiidräbu ka väävlisse, kulutades taas sferoidiseerivaid elemente, kiirendades sferoidiseerimise langust ja mõjutades veelgi sferoidiseerumise kiirust. Kõrge sferoidiseerumise määra saavutamiseks tuleks toores rauas sisalduva ω (S) kogus vähendada alla 0.02%.
4.2 Väävlitustamistöötlus
Pärast laengu sulamist võtke proovid ja analüüsige keemilist koostist. Kui ω (S) kogus on suurem kui 0.02%, on vajalik desulfureerimine.
Naatriumvesiniku desulfureerimise põhimõte on: asetage kulbile teatud kogus sooda, loputamiseks ja segamiseks kasutage sulatatud raua voolu, sooda laguneb kõrgel temperatuuril, reaktsioonivalemiks on Na2CO3 = Na2O + CO2 ↑: tekkinud Na2O on taas sulavas rauas Na2S, (Na2O) + [FeS] = (Na2S) + (FeO) vääveldumine ja moodustumine.
Na2CO3 eraldab ja lahutab CO2, põhjustades sulanud raua vägivaldset segamist, mis soodustab desulfureerimisprotsessi. Soodatuhka räbu on lihtne voolata ja hõljuda ning väävlitustamise reaktsiooniaeg on väga lühike. Pärast desulfureerimist tuleks räbu õigeaegselt eemaldada, vastasel juhul naaseb see väävlisse. 4.3 Dezoksüdatsioonieelne töötlus, sferoidiseerimine ja inokuleerimistöötlus Foseke 390 eeltöötlusaine mängib kotis deoksüdatsioonieelse ravi rolli ja suurendab samal ajal grafiidi tuumasüdamikku ja grafiidikerade arvu pindalaühikus ning võib ka suurendada Mg imendumiskiirust. Parandage märkimisväärselt majanduslanguse vastu seismise võimet ja suurendage sferoidiseerumise määra. Fochke inokulant sisaldab ω (Si) = 60% ~ 70%, ω (Ca) = 0.4% ~ 2.0%, ω (Ba) = 7% ~ 11%, millest Ba võib pikendada efektiivset inkubatsiooniaega. Valitakse Fozco Nodulizer NODALLOY7RE klass ja selle ω (Si) = 40% ~ 50%, ω (Mg) = 7.0% ~ 8.0%, ω (RE) = 0.3% ~ 1.0%, ω (Ca) = 1.5 % ~ 2.5%, ω (Al) <1.0%. Kuna sulatatud rauas toimub desulfureerimine ja deoksüdeerimiseelsed protseduurid, on sulatatud rauas sõlme tarbivaid elemente oluliselt vähendatud, mistõttu sfäärilise grafiidi morfoloogia halvenemise vähendamiseks RE-ga valitakse madala ω (RE) kogusega nodulaator ; Tegevuse põhielement on Mg; Ca ja Al võivad mängida rolli inkubatsiooni tugevdamisel. Ränikarbiidi ja ferrosilika kombineeritud inokulatsioonravi abil on ränikarbiidi sulamistemperatuur umbes 1600 ° C ja tahkestumisel suureneb grafiitkristalli tuum ning inokuleerimiseks kasutatakse suuri ferrosilikooni annuseid, mis võivad takistada sferoidiseerimise vähenemist.
5i kokkuvõte
Ferriitilise nodulaarse malmi tootmisel, kui sferoidiseerumismäär peab olema üle 90%, võib võtta järgmisi meetmeid:
- (1) Laadis olevate sferoidiseerimiselementide vähendamiseks valige kvaliteetne laeng.
- (2) Valige sferoidiseeriv aine, mille ω (RE) sisaldus on väike, et vähendada RE halvenevat mõju sferoidgraafiidi morfoloogiale.
- (3) Algse sulanud raua ω (S) sisaldus peaks olema väiksem kui 0.020%, mis võib vähendada nodulaatorite tarbimist, eriti sulfiidse räbu sekundaarsel vääveldamisel tarbitud sõlmede elementide tarbimist.
- (4) Deoksüdeeritakse sulatatud raua, suurendatakse grafiitkuulide arvu pindalaühikus, suurendatakse sferoidiseerumiskiirust, parandatakse oluliselt majanduslangusele vastupanu ja pikendatakse efektiivset inkubatsiooniaega.
- (5) Vähendage ω (Si) kogust algses sulatatud rauas, suurendage sferoidiseeriva aine, inokulandi ja mitmesuguste eeltöötlusainete hulka ning tugevdage inokuleerimist.
Palun hoidke artikli printimiseks allikas ja aadress: Kuidas parandada sferoidiseerumiskiiruse valamisprotsessi mõõtmeid
Minghe Survevalu ettevõte on pühendatud tootmisele ja pakuvad kvaliteetset ja suure jõudlusega valuosasid (metallvaluosade valikusse kuuluvad peamiselt Õhukese seinaga valuvorm,Kuum kambris valamine,Külmkambris valamine), Ümmargune teenus (stantsimisteenus,CNC mehaaniline töötlemine,Hallituse valmistamine, Pinnatöötlus). Mis tahes kohandatud alumiiniumist valuvorm, magneesium- või Zamak / tsinkvaluvorm ja muud valandid on teretulnud meiega ühendust võtma.
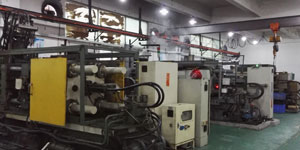
ISO9001 ja TS 16949 kontrolli all viiakse kõik protsessid läbi sadade täiustatud survevalumasinate, 5-teljeliste masinate ja muude seadmete kaudu, alates lõhkajatest kuni Ultra Sonicu pesumasinateni. Minghe'l on lisaks täiustatud seadmetele ka professionaalsed seadmed kogenud inseneride, operaatorite ja inspektorite meeskond kliendi disaini teostamiseks.
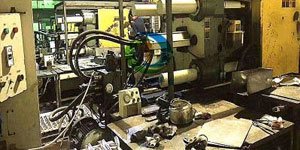
Valuvormide lepinguline tootja. Võimalused hõlmavad külmkambri alumiiniumist valuvorme alates 0.15 naelast. kuni 6 naela, kiire muutmise seadistamine ja töötlemine. Lisaväärtusega teenused hõlmavad poleerimist, vibreerimist, korrastamist, lõhkamist, värvimist, plaadistamist, katmist, kokkupanekut ja tööriistu. Materjalid, millega töödeldi, sisaldavad sulameid nagu 360, 380, 383 ja 413.
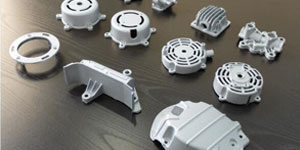
Tsinkvaluvormide projekteerimise abi / samaaegsed inseneriteenused. Tsingitud täppisvalu kohandatud tootja. Valmistada saab miniatuurseid valusid, kõrgsurvevalusid, mitme slaidiga valuvormi, tavapäraseid vormivalusid, ühtseid ja iseseisvaid valusid ning õõnsusega suletud valusid. Valusid saab valmistada pikkuste ja laiustega kuni 24 tolli tolerantsiga +/- 0.0005 tolli.
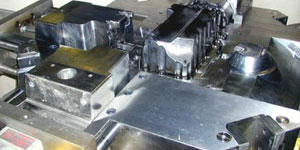
ISO 9001: 2015 sertifitseeritud valatud magneesiumi tootja. Võimalused hõlmavad kuni 200-tonnise kuuma kambri ja 3000-tonnise külmkambri kõrgsurvevalu valamist, tööriistade kujundamist, poleerimist, vormimist, töötlemist, pulbri- ja vedelvärvimist, täielikku kvaliteedi tagamist CMM-võimalustega , kokkupanek, pakendamine ja kohaletoimetamine.
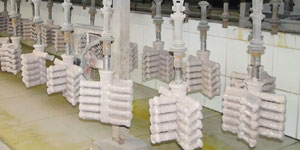
ITAF16949 sertifitseeritud. Täiendav ülekandeteenus sisaldab investeeringute valimine,liiva valamine,Gravitatsioonivalu, Kadunud vahu valamine,Tsentrifugaalvalu,Vaakumvalu,Püsiv vormivaluVõimalused hõlmavad EDI-d, inseneriabi, kindlat modelleerimist ja teisest töötlemist.
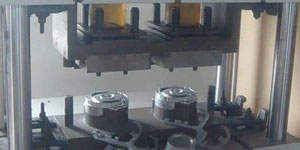
Casting Industries Osade juhtumianalüüsid: autod, jalgrattad, õhusõidukid, muusikariistad, veesõidukid, optilised seadmed, andurid, mudelid, elektroonikaseadmed, ümbrised, kellad, masinad, mootorid, mööbel, ehted, rakised, telekommunikatsioon, valgustus, meditsiiniseadmed, fotoseadmed, Robotid, skulptuurid, helitehnika, spordivarustus, tööriistad, mänguasjad ja palju muud.
Mida saame aidata teil järgmisena teha?
∇ Mine kodulehele Die casting Hiina
→Osade valamine-Uurige välja, mida me oleme teinud.
→ Ralated Tips About Die casting teenused
By Minghe Die Casting Tootja Kategooriad: Kasulikud artiklid |MATERJAL Sildid: Alumiiniumvalu, Tsingi valamine, Magneesiumivalu, Titaanivalu, Roostevabast terasest valamine, Messingivalu,Pronksivalu,Video ülekandmine,firma ajalugu,Alumiiniumi stantsimine | Kommentaarid on välja lülitatud